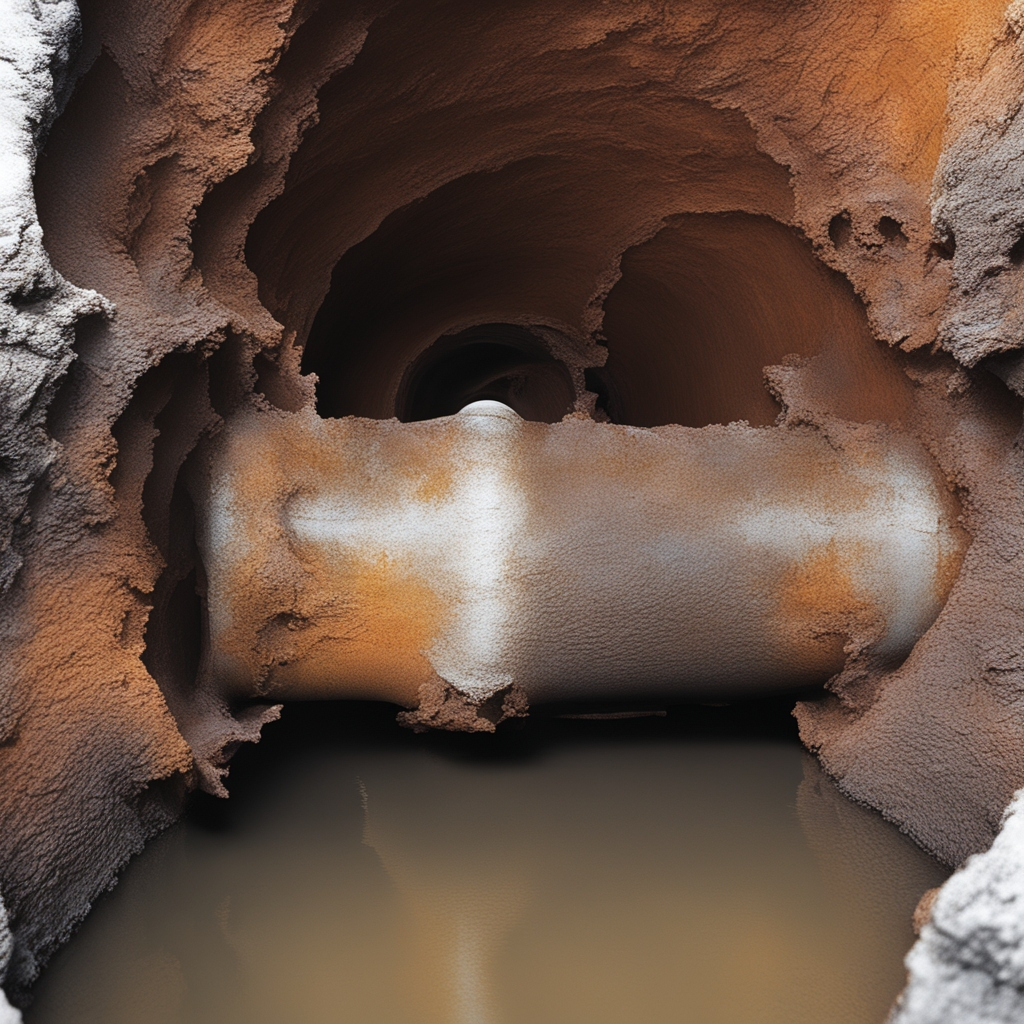
Internal Corrosion Direct Assessment (ICDA) is a structured process that improves safety by assessing and reducing the impact of internal corrosion on pipeline integrity. “ICDA” proactively identifies the corrosion defects and prevents them from growing to a size that would ultimately compromise the structural integrity of the pipeline.
- Remediating the causes of corrosion
- Repairing and preventing further corrosion
- Identify and address corrosive activity along the pipeline.
Internal Corrosion Direct Assessment is based on a detailed examination of key locations in the pipeline structure, electrolytes such as water are collected first and provide information about the remaining length of the pipe. The main purpose of this approach is to determine if internal corrosion can occur on pipes of the selected length. The locations where electrolytes are most likely to accumulate are predicted using the results of pipeline multi-phase flow modeling. If areas along the length of the pipe that are most likely to collect electrolytes are not corroded, other areas that are unlikely to collect electrolytes can be considered non-corroded and need no further investigation. There is none. The method is applicable for gas transmission lines that normally carry dry gas but may suffer from short-term upsets of wet gas or liquid water.
Through regular assessments, pipeline operators can easily identify and address the locations where corrosion has occurred, is occurring, or may occur. The internal direct assessment of a pipeline involves the following phases through the process:
Pre-Assessment of structure
The ICDA pre-assessment phase involves:
- Collecting the necessary operational data to properly perform multi-phase modeling
- Planning the collection of field data during the indirect inspection phase
- Collecting historical and operational data regarding the pipeline to assure that the ICDA methodology is appropriate for the particular pipeline
In-direct Assessment of structure
Utilizing the sub-meter, accurate GPS, and a pipeline current mapper tool to collect accurate depth of the cover data, a pipeline elevation profile is created from data collected along the pipeline. This data, in conjunction with the multi-phase flow modeling calculations determined by our liquid hold-up software, allows for critical inclination angle locations to be identified as potential water hold-up locations.
Direct Inspection of structure
Based on the model results developed in the indirect inspection, multiple excavations can be performed to allow for direct physical examination of the predicted hold-up points. Ultrasonic thickness testing of excavated pipelines is conducted to assess whether internal corrosion at these breakpoints is a current threat.
Post evaluation
In this step, CONSULTECH outlines the findings, evaluates the effectiveness of the ICDA process, and produces a detailed report recommending re-evaluation intervals.
Consultech - Internal Corrosion Direct Assessment Service
CONSULTECH has performed ICDA assessments for a large number of pipelines according to the NACE Standard SP0206-2006 Dry Gas Internal Corrosion Direct Assessment (DG-ICDA).
CONSULTECH’s qualified technical staff can perform and analyze the results of each phase of the pipeline’s internal corrosion assessment.
Benefits of using Consultech:
- Experience with various kinds of cathodic protection systems spanning over 58 years
- Cathodic protection system testing, installation, and upkeep experience for all kinds of structures globally
- NACE corrosion engineers and professionals with high levels of training
- team members with prior client-side CP project expertise
- having experience leading corrosion divisions of big utilities and pipeline industries and multimillion-dollar CP projects
- Compared to certain regularly used CP systems, Consultech’s several unique cathodic protection technologies are more affordable and have longer lifetimes.
Your corrosion issues are CONSULTECH’s primary concern. In addition to project management and comprehensive turnkey solutions, we are prepared to help with your requirements for corrosion engineering and field service, including design, production, installation, commissioning, and continuing maintenance. Additionally, we provide a huge selection of unique corrosion protection materials.